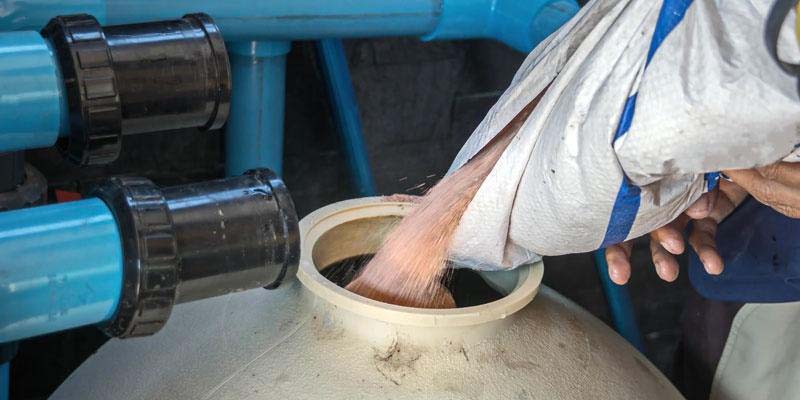
While well intervention spending has been hit harder than average industry cuts, the opportunities are still there to be had, not least from mature North Sea assets, delegates at Offshore Network’s Offshore Well Intervention Europe Conference heard this morning.
But, companies need to have the right attitude, processes and resources in place to get what could be double digit percentage increases in production that could be achieved. They also need to increase well intervention intensity and use a broad range of tools to benefit the most, says Dan Cole, General Manager, Energy Insights, McKinsey & Company. Setting out the industry context, Cole says: “We have been at $50/bbl or so for a year, more or less, and there are signs investment is starting to pick up. But it is hard to ignore the backdrop. A third of the cost has been taken out of the sector since its peak in 2014. Spending levels are the same as they were seven years ago. North Sea well maintenance spending has seen an even greater decrease, down 43%, from $1.3 billion in 2014*. Could it be the opportunity is not there? Absolutely not.”
To see what exactly the opportunity is, McKinsey looked at various metrics. One was the number of shut-in wells, relative to their maturity, measured by water cut. “There are more shut-in wells as fields become more depleted and have higher water cut,” he says. “One in five depleted wells are shut-in, some permanently. But if some could be restored to a level similar to [comparable] onstream wells, you could very quickly get some good production numbers. From a rough calculation, you could get to a couple of hundred thousand barrels of oil equivalent a day production [across the North Sea].”
Another metric McKinsey looked at was production losses, i.e. maximum production capacity compared with actual production. The losses are split into two categories: reservoirs losses, i.e. where a well is not producing as expected, maybe due to mechanical impairment, sand inflow, lack of pressure support, etc.; and losses incurred due to well work, i.e. testing and intervention work.
“From 2008-12, the amount of losses incurred increased year on year and peaked in 2012 (partly driven by the Elgin Franklin well control incident),” Cole says. “Since then, every year has seen fewer losses. The share of the losses has also moved from reservoir losses to losses due to well work [i.e. testing and intervention work], which is encouraging to see.”
The industry also knows more now about what better well work and reservoir management looks like, through more experience and benchmarking. Examples can be given which show that when two operators with similar assets are compared, the one which performs more interventions and with a wider range of intervention tools and techniques sees greater production increases than the other.
McKinsey compared two such operators, one who intervened in one in 15 wells and the other one in three. The second had 9-10% increase in production, compared with 2% on the first. “Consistently, operators with higher levels of intervention and production use a broader range of intervention tools,” says Cole. “Add a broader range of tools and more intensive intervention levels drives overall better performance around well intervention and reservoir management.”
By seeking additional recovery, restoring shut-in wells, improving reservoir management, increasing the ratio of water injection and doing infill drilling (increasing the number of wells per reservoir), could bring $70-350 million additional returns in the first year, says Cole, according to studies by McKinsey. Cole says he’s been talking to operators recently which have been getting 5-7% increases from wells that are years and even months from their cessation of production date.
Previous work the firm has done has shown that well intervention can give higher – and faster – rates of return on investment. “We found, as a portfolio activity, intervention stacked up very well against drilling on payback time and also on over all returns, at about 1.5 X better then drilling,” Cole says.
McKinsey has also looked at the difference between companies with successful intervention programs and those that are less successful. “Typically, the difference between the good and the not so good are; differences in technical system, i.e. the process side; the organisation and how it is organised; and the philosophy or attitudes towards the activity,” Cole says. “Making sure there is a process in place, identifying the opportunities and getting them through the operation, performance tracking and a good way to transfer knowledge between jobs that go well and those that fail,” all help to put the process in place, he says. “It also matters, having an organisation lined up around this and you need clear responsibilities, key performance indicators and targets as resources – cash and capability. It is also important that they [decision makers] understand this is a core part of the business and considered at the top level. We know some interventions fail and some are extremely successful. The success rate overall is more than 50%, but people remember the ones that fail. That needs to be challenged.” Poor plant reliability and poor execution of interventions also results in poor performance in this area he says. “To get this activity humming, you need all of the cogs to work,” he says. The North Sea industry could also learn from outside Europe, including the way onshore North America operators “ruthlessly” approach their wells.
Offshore Network’s event, being held in Aberdeen, continues today and tomorrow.
*Based on data from across 50 assets in the Norwegian, UK and Danish sectors of the North Sea.