Europe
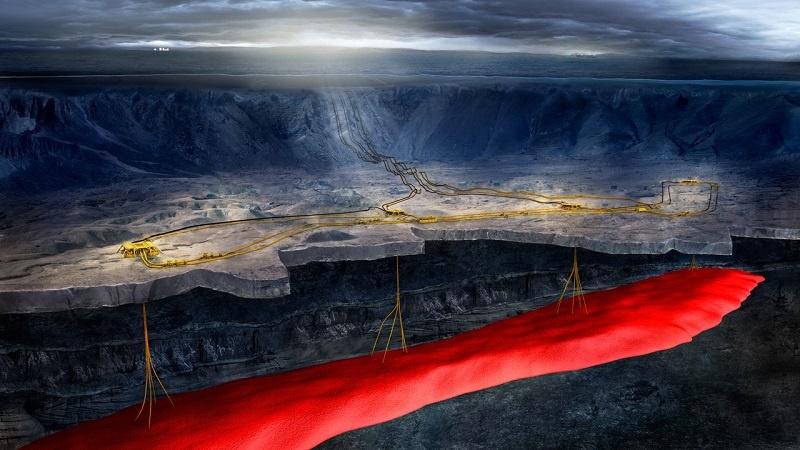
- Region: North Sea
- Date: July, 2021
A/S Norske Shell has utilised Kongsberg Digital’s digital twin solution Kognitwin Energy to create a virtual representation of their Ormen Lange deepwater gas field which was released to users last month.
Feeding into the onshore digital twin developed at Nyhamna gas processing facility, the two will be combined to become the first ever fully integrated reservoir to market digital twin.
In October 2019, Norske Shell collaborated with Kongsberg Digital to operationalise an ‘asset of the future’ through a partnership development of the Nyhamna Dynamic Digital Twin, using Kongsberg Digital’s Kognitwin Energy solution. By the end of the year the solution was operational and since January 2020 the Nyhamna Dynamic Digital Twin has been evolving continuously through monthly product releases, focusing on safe, effective and integrated work processes and the optimisation of production and energy use. With Nyhamna having paved the way, the decision was made to expand the collaboration with another digital twin of the related Ormen Lange deepwater gas field, which feeds gas to Nyhamna.
Ormen Lange
Hege Skryseth, President of Kongsberg Digital and EVP Kongsberg, said, “With Ormen Lange, we are very proud to have been awarded the contract for the development of a second digital twin for Norske Shell. This is a direct result of our successful collaboration around the Nyhamna dynamic digital twin. We would particularly like to highlight a strong core product, Kognitwin Energy, rapid deployments, and fast time to value as unique differentiators in this ongoing project. Now, we are eager to help Norske Shell realise the full potential of their assets through integration of these two digital twins.”
The first version of the Ormen Lange digital twin comprises primarily data integrations and visualisation of subsea 3D models including production and MEG pipelines, well surface locations and well-bore paths, seabed bathymetry data detailed around the production templates, built documentation and drawings, real time data from DCS and PI and much more. For disciplines and teams across the initial Ormen Lange user base the twin provides unified data for everyone to access across the same work surface.
Rolf Einar Sæter, Digitalisation Manager in Norske Shell, commented, “Digital twins are technology for people. The partnership model, combining Kongsberg Digital’s digital capabilities with our own employee’s expertise in the operations and maintenance domain, has been very effective in delivering use cases that let our teams to collaborate better and become more effective. This in turn enable us to save costs and optimise production whilst improving safety and environmental impact.”
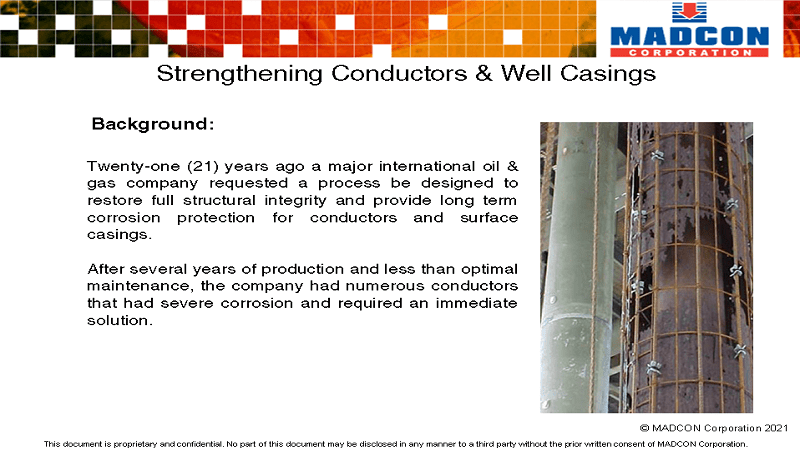
- Region: North Sea
- Topics: Integrity
- Date: June, 2021
Speaking at the Virtual Offshore Well Intervention Europe Conference 2021, Bruce Trader, President of MADCON Corporation, guided an audience through his company’s Structural Composite Retrofit (SCR) process, developed to restore the structural integrity of conductors and well casings as well as providing long term corrosion protection.
Trader explained how the process was conceptualised after a major international oil and gas company requested a process to restore the integrity and provide long term corrosion production for their conductors and surface casings as they had been experiencing several years of less than optimal performance. The company had numerous conductors that all were suffering from severe corrosion and required an immediate solution.
For this to be a success, the company issued several key mandates which MADCON had to fulfil including:
-Restore the original design capacity
-Allow future work
-Minimal to zero hot work
-Long term corrosion protection
-Ease of installation in the splash zone
-Meeting regulators compliance
-No cofferdam required
-Fit within the existing conductor guides
-Conduct the work from vessels or the platform and not require a barge or rig
-Eliminate the need for future maintenance.
When the operator hired a third party engineering company to analyse and validate the method MADCON put forward, they assumed that there was no remaining conductor wall or inner string pipe capacity and that the composite section had to be designed to take the full axial and bending load.
Trader explained the basic SCR process which they followed to help the operator, which begins by, if the surface casing is not already grouted, grouting the surface casing annulus to a select elevation (in this case 2-3 metres below the water). This consists of installing a plug to isolate the annulus and putting on epoxy grout before finishing with cement grout all the way up to the wellhead (there is no need to grout to the mud line as the corrosion is not severe a couple of metres below the water). If there is a large length of unsupported casing a reinforcement cage made may be required before, in the final step, a fibreglass jacket is installed to be pumped full of epoxy grout from the bottom up.
As one of the key mandates was to install in splash zone, the materials were all lightweight, composite and easy to install. In more than thirty years of conducting these operations MADCON has recorded zero incidents for the divers involved.
In order to keep hot work (and by extension expense) down, MADCON also took pains to make the repair within the existing conductor guides. The platform had a tight space which posed a challenge but this was able to be overcome and today the company’s repairs only add 1-3 inch in overall diameter meaning they can perform repair work within most existing guides out there saving time, money and eliminating hot work. The company additionally captured more value by performing the work without the use of a rig or large barge as they are able to perform the repairs with relatively small vessels of opportunity or even the platform itself.
Summarising this job, Trader said, “We were able to achieve all the mandates stipulated by the operator including, once the repair was done, eliminating future maintenance so that 27 years (and counting) after the repair everything is still in perfect condition.”
Reliable performance
After gaining a formidable reputation for this kind of work, operators even began commissioning the company for wells that had corroded so much to the point where the surface casing had collapsed. But, as Trader demonstrated with a string of case studies to conclude the session, this was not an issue but something they have now come to specialise in.
For one well, for instance, prior inspection posted no abnormal operational conditions but an inspection from MADCON identified that in fact the well had in fact collapsed and had to be shut in. The company then dissected and removed some of the conductor pipe and identified that the conductor to surface casing was open at a certain elevation and, without anyone knowing, it had been slowly corroding the surface casing to the point that it failed. While supporting the well with casing jacks, the MADCON crew of 8 techicians were able to perform full structure repairs from the platform, from -3 to +20 metres, in just 12 days. Once done the operator was able to get his well back online and producing again.
Trader said, “This process can be modified to restore any capacity that the operator might need and we have been successfully using it to restore original design capacity and provide long term corrosion protection on hundreds of wells.”
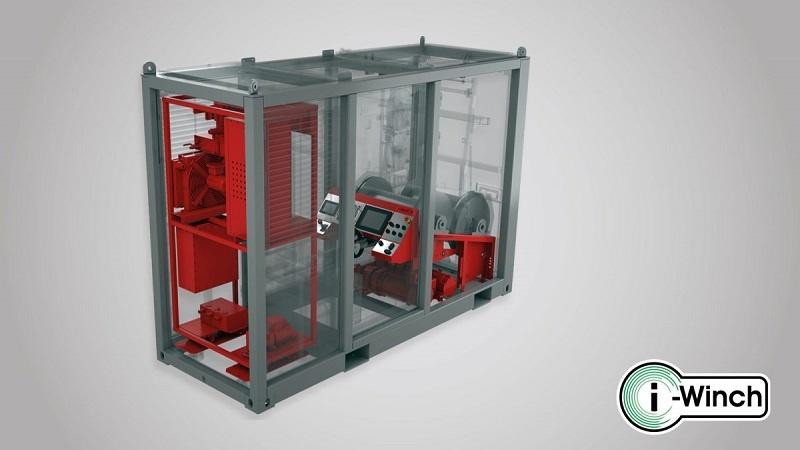
- Region: All
- Date: June, 2021
Paradigm, an upstream oil and gas technology and services company, has launched the i-Winch, a sustainable conversion service for adapting existing diesel hydraulic intervention winches to fully electric driven intelligent winches.
The i-Winch was developed from their fully electric driven and controlled E-Winch range, to address the challenges facing service companies to invest in new assets that offer lower carbon solutions.
“With the current pressures on oil and gas companies to reduce carbon emissions, the benefits of electric driven winch systems are clear. As with the uptake of electric cars with environmentally conscious consumers, so too are operators looking to satisfy their need to responsibly reduce emissions,” commented William Ash, Managing Director of Paradigm Technology Services, a division of Paradigm Group.
“We developed the i-Winch unit based on a philosophy of repurposing existing diesel hydraulic winches into fully electric drive units, using our proprietary drive system which eliminates the need for hydraulics in either diesel or electric hydraulic driven winches.”
Capturing value
Ash continued, “One of the major challenges for service companies currently is the investment costs involved in switching to electric driven units whilst they already have a fleet of conventional diesel hydraulic units on the books. For example, one of the most prolific winches on the market over the years is the ASEP SlimLine, a diesel hydraulic designed unit designed to last several decades. An i-Winch conversion to rebuild an old unit back to fully electric driven, will extend the life of the unit by at least 10 years, so not only extending the life of the unit but eradicating the need to repair or replace equipment.”
“In addition, the performance of the unit is improved and offers all the benefits of our E-Winch range with constant speed or tension control, remote control, automated jarring, zero-line breakage, and enhanced safety whilst being fully configured for remote operations, thus reducing the number of crew. We conservatively estimate US$15,000 annual maintenance saving per unit after the conversion whilst sustainably repurposing a significant portion of the material from the donor unit as part of the process”.
Ash concluded, “Operators are under pressure to significantly lower their carbon emissions right now, and we are proud that our values and global leading technology combine to offer a cost-effective solution here. The combination of our E-Winch or i-Winch units with our digitally enabled slickline platform system, Slick-E-Line, can transform conventional well intervention operations into a fully digitally enabled well intervention single package, that reduces runs, reduces costs and reduces carbon impact whilst enhancing real time control.”
For a relatively young company (Paradigm Group was established in 2009) the i-Winch unit is the latest in a strong line of solutions developed to minimise carbon impact and generate value for the energy industry.
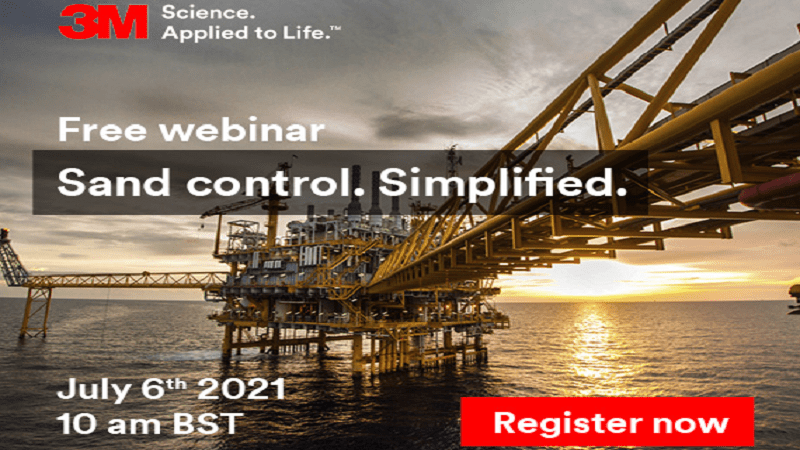
- Region: North Sea
- Date: June, 2021
As part of the Offshore Well Intervention Virtual Offshore Well Intervention Europe Conference 2021, Charles Sanders, Business Development Manager at 3M, explained how 3M’s Ceramic Sand Screen Systems can provide operators and service companies with a competitive advantage and better risk/reward profile for well intervention operations.
Sanders opened the session by describing the basic design of the ceramic sand screens. The equipment is made up of a perforated base pipe with ceramic rings placed over on top. These rings have ridges that create a profile and provide the sand control. The solution comes in modules of 1.5m length and is available in a range of different sizes.
Alongside a host of benefits, the ceramic sand screens have been designed to reduce and potentially nullify three main areas of risk: erosion, economic and reputational.
Explaining these, Sanders noted that because the through-tubing of the sand control solution has been designed with reduced tubing size there is a perception that it is therefore higher risk as it amplifies the erosional forces at previous economic flow rates. But this is only the case with standard screens using inferior material which are severely limited by their susceptibility to erosion. With such equipment, when dealing with erosive material, the operational velocity must be kept fairly low otherwise the well life can be greatly shortened.
By replacing the traditional materials with ceramic, which is highly resistant to erosion and corrosion, the root cause of these problems are addressed which completely changes the traditional rule of thumb to indicate whether a screen can be run.
Sanders commented, “The material change in our sand screens means we can push the intermediate boundary so that conditionals viewed as high risk with traditional materials are now low risk. We have deployed into harsh environments far and excess of what the rule of thumbs are. This will enable us and operators to be more competitive and change the risk/reward landscape.”
A well that is producing to its full potential, unhindered by solids production, is a future revenue stream for both operator and service company. In this way the ceramic sand screen reduces the erosion risk, as explained; reduces the economic risk, by offering enhanced produce rates as well as limiting the cost of failure; and reduces reputation risk both on a corporate and personal basis, as 3M’s proven track record with this technology means you can be confident when deploying it.
Ceramic Sand Screen case studies
To demonstrate the capabilities of the ceramic sand screens, Sanders guided the audience through three case studies where the technology has been deployed.
The first was covering an underperforming gas well in the North Sea where it was not feasible to do a frac pack. There were no sand management facilities on the platform and the estimated velocity in perforations was 100 ft/s. 3M deployed their ceramics sand screens for the frac operation at 3 screen joints using rigless on E-line single run through the riser. This resulted in no proppant flow back for all six sub sea and two platform well applications, high rates of 35 MMSCFD, and increased longevity of the well life with all still producing today with no sand control failure.
After this success, 3M wanted to deploy their technology to enter into different zones and were commissioned to provide a cost effective solution to maximise production from a well in a shallower zone with downhole sand control in Egypt. This well had high gas rates, high influx velocity and impingement velocity through short net target zone. Hot spotting was also a major concern. Ceramic sand screens were chosen to address these challenges, and via a rigless wireline deployment, they were placed across the perforation zone in two wells and two wells above the perforation zone inside the tubing. This added 15 MMSCFD of gas to the asset, achieved sand free production rates and the company subsequently reviewed the technology to replicate it as the primary sand control method in other applications. As a result of these benefits the operator was able to capture more than US$12mn in first year of average production.
Finally, Sanders described an example in Norway where the ceramic screen was used for OH SAS completions in high corrosive and high rate gas wells. The solution in this case was specifically designed to address client specific OH challenges. Once deployed the sand screens eliminated the technical challenges and risks of gravel packing HPHT conditions, reduced the operation risk and avoided the cost of pumping services. Subsequently, the well was able to achieve its target rate of 106 MMSCFD.
Sanders added that the velocity encountered on these wells (such as 100 ft/s at the North sea operation) was huge and something that could not even be considered by traditional sand screen methods and yet 3M’s solution coped effectively and has even been tested in environments of up to 200ft/s. This represents a significant step change.
Sanders stated, “When you remove the risk perception the high risk opportunities open up. I have focused on erosional environments and benefits here but there is a whole range of advantages that this solution offer such as reduced operational complexity and HSE risks, proven productivity and minimised solids production, rationalising and standardising effective control design in the field, and can save you up to four to six times of CAPEX requirements over a conventional rig operation.”
Concluding the session, Sanders offered the audience the opportunity to challenge 3M with their well sand problems which they would be happy to look into and address if they can. As Sanders added, “these don’t solve every problem, but they sure do solve a lot of them and we would love to see how we can help deliver better performance for your assets or well intervention services.”
Another opportunity to learn more
On Tuesday, July 6th 2021, 3M will be demonstrating in more detail how the Ceramic Sand Screen Systems can offer effective sand control and long term productivity for your wells in a free online webinar.
Starting at 10:00 am BST, 3M will discuss whether the current sand control practices used in oil and gas production contribute enough to meet productivity targets and energy policies, and explain how 3M’s ceramic sand screens can eliminate the need for complex sand control methods. This will be followed by a Q&A session where you can ask your questions anonymously. If you register and can't make it to the webinar, a recording is available after the event.
To sign up, follow the link below:
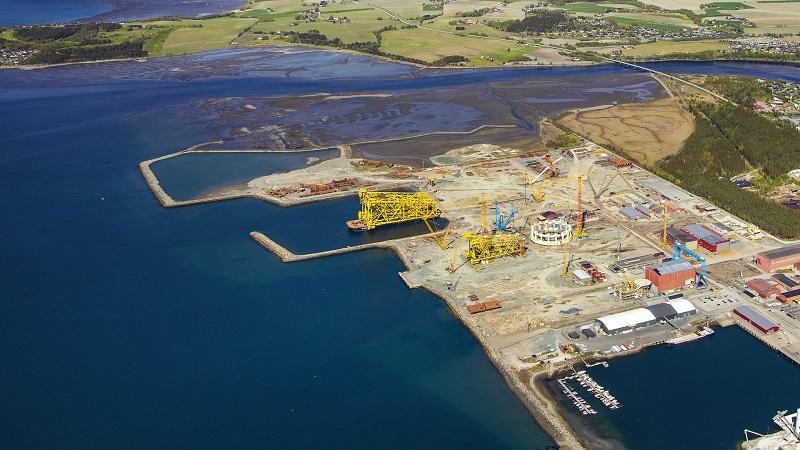
- Region: North Sea
- Date: June, 2021
Aker Solutions has delivered another steel substructure for the largest industry project ever in Norway, the Johan Sverdrup field.
For phase 1 of the project the company previously provided three platform jackets and, with this jacket for phase 2, four out of a total of five have now been built and delivered on time and budget from Aker Solutions’ yard in Verdal, Norway.
Through the frame agreement entered into in 2014, and in international competition, Aker Solutions was awarded three out of four jackets for the first phase of the project. The first delivery was the riser platform jacket in the summer of 2017 which was the largest and most complex platform jacket delivered from Aker Solutions to date. It was delivered alongside the first visible installation at the new Johan Sverdrup field centre. In March 2018, Aker Solutions delivered the steel substructure for the drilling platform, and in July of that year the process platform substructure was delivered.
Now Aker Solutions has announced that the process platform substructure for phase 2 is en route from Verdal.
Sturla Magnus, Executive Vice President and Head of Aker Solutions' topside and facilities business, said, "This is an exciting and important day for us. Through great cooperation with Equinor, we have delivered all four of these platform jackets at the agreed quality, time and budget. I am very pleased that our customers confirm that we are a supplier that offers an attractive combination of technical expertise and cost-effectiveness.”
In total, the deliveries from Aker Solutions in Verdal make up about 90% of the total weight of the substructures for the combined phase 1 and 2 of the Johan Sverdrup field. More than 100,000 metric tons of steel will be delivered from Aker Solutions' facility in Verdal, including the piles that attach the jackets to the seabed. In addition, Aker Solutions’ facility at Stord has delivered a topside as well as a large module for the Johan Sverdrup field.
Erik Stiklestad, Aker Solutions’ Yard Director at Verdal, commented, “We have extensive experience in providing the customers with complete and seamless deliveries. In recent years, we have also increased industrialisation for how we execute projects. This, combined with long-term relationships in the supplier market, makes it possible for us to offer flexibility to our customers. We are now delivering as planned despite a year of major challenges with Covid-19. Together with our employees and partners, we have found good solutions that enable us to deliver the jacket to our customer Equinor without serious injuries during the execution.”
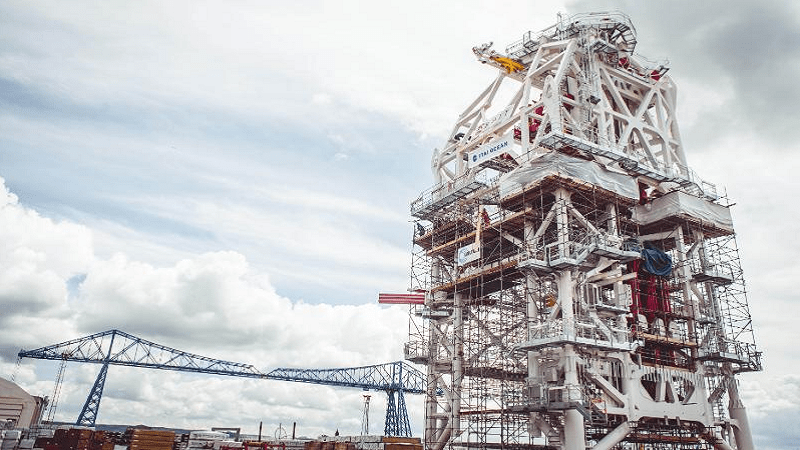
- Region: North Sea
- Date: June, 2021
Offshore technology supplier Osbit Ltd has reached a key milestone in the assembly of a new well intervention tower system for FTAI Ocean.
The FTAI Ocean Smart Tower System now stands at 40 metres (its full height), after the top section of the tower on to the lower section was installed in a complex lift operation.
This involved hoisting the top section of the tower by crane and holding it in place on the lower section, while the sections were welded together. With the two sections joined together, the final fitout of hydraulic, control and electrical parts can now take place.
The FTAI Ocean Smart Tower System
The system, currently under construction at Wilton Engineering Services in the UK, will facilitate integrated riserless and riser-based well intervention operations on FTAI Ocean’s flagship DP3 vessel M/V Pride. When completed, it will weigh 1,300 tonnes and be capable of operating in water depths up to 1,500 metres.
It integrates a series of innovations derived from Osbit’s experience in developing well intervention and offshore handling equipment to improve operational safety, flexibility, and accessibility:
-The tower’s vertical Open Water Intervention Riser System (OWIRS) racking system improves deck safety by reducing the need for access around the well centre to handle OWIRS joints, while its small footprint optimises deck space, for more effective equipment storage.
-The system integrates the existing vessel crane into the full deployment system, providing up to a 250-tonne active heave compensated capacity. Additionally, the system offers an active and passive heave compensated platform for building, operation, and recovery of OWIRS, and riser based or riserless intervention systems in 1,500 metres and 3,000 metres respectively. The heave compensated platform is able to support coil tubing, slickline and e-line operations and provides safe and efficient personnel access via an integrated walk to work system.
-The system is fitted with both guide wire and pod wire systems which, alongside the deck skidding system, minimises the need for crane lifts, increases operating windows and enables equipment to be directly loaded into the well centre.
-Also incorporated is Osbit’s Integrated Logistics Support (Osbit ILS) software technology, which offers detailed data insight and asset performance analysis.
Steve Bedford, Director at Osbit, commented, “This system is the culmination of our extensive expertise and strong reputation in the design and build of cutting-edge well intervention and offshore handling systems. We remain committed to utilising our capabilities to support our clients in enabling safer and more efficient offshore operations.”
“As a business, it is rewarding for us to see this world-class piece of kit successfully coming together and we are very much looking forward to delivering the completed system to FTAI Ocean.”
Jon Attenburrow, Managing Director at FTAI Ocean, added, "This is a great achievement, for all involved in the design, build and assembly of the Smart Tower System, in these difficult times. We are pleased the build has been carried out safely and professionally to date, and look forward to the successful completion of the world class Well Intervention Tower.”
To hear more from Osbit and industry experts on the latest technology and best practice relating to well intervention, be sure to attend the Offshore Well Intervention Europe Virtual Conference 2021 which is accessible via this link: https://www.offsnet.com/owi-eu/register.
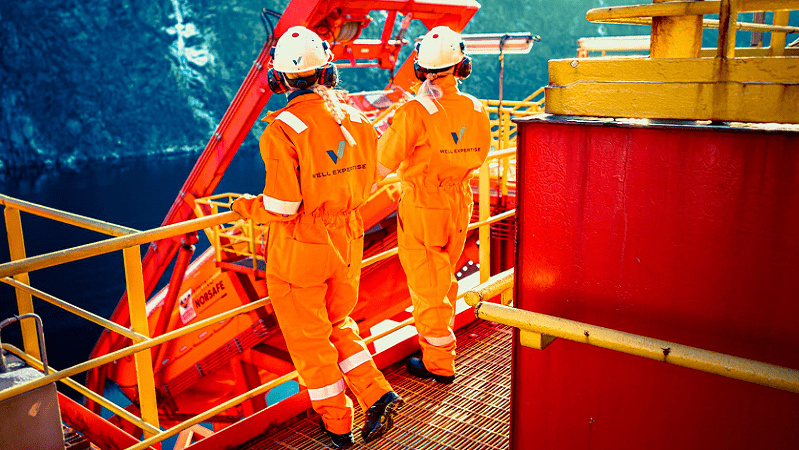
- Region: North Sea
- Date: May, 2021
Well Expertise, a well management company providing well planning and operational support, has successfully used a mobile simulator for plug and abandonment (P&A) well control training to decommission several wells in the North Sea.
Well Expertise is the well management company for operator DNO during planning and execution of the permanent plugging and abandonment (P&A) of three subsea template wells at Oselvar.
Well Expertise worked closely with Drilling Systems and training specialist Survivex to develop high level well specific scenarios to simulate bull heading, reverse circulation, trapped gas and cutting casing operations. Six crews were then given various scenarios to test choke control and response to pressure increases.
This is the first time an on-the-rig (OTR) simulator has been used in-situ for P&A well-specific training to help prepare crews in advance of potential well control situations in the operation.
Following this and previous onboard simulator training success, Well Expertise will now be rolling out well specific onboard simulator training across its remaining drilling campaigns later this year with DNO, Wellesley and other operators.
Morten Laget, Business Development Manager at Well Expertise, commented, “We have an exceptional record of risk management and safety is our top priority. We strive to offer our clients any solution available that helps to reduce the risk of the operation and onboard simulator training is an excellent tool to help with this.”
“Killing the well is a key part of any decommissioning project and presents its own unique challenges. Plug and abandonment training is typically not addressed to this extent during periodic mandatory well control courses, but the OTR equipment allowed us to undergo some practical training on the rig itself during work time combined with review of subsea equipment and associated operations. This helped the crew in building competency and confidence and lowering the risk of major well control incidents,” Laget added.
Clive Battisby, Head of Simulation at 3t Energy Group, said, “The strength of the 3t Energy Group lies in our holistic offer, which combines cutting-edge technology with the very best of traditional training. For Well Expertise we combined tailored simulator training in-situ with experienced instruction to deliver a blended learning solution to meet the client’s needs.”
“To our knowledge this is the first-time blended learning with the OTR has been delivered for a P&A campaign and we are delighted it has worked so well. We are looking forward to working with Well Expertise again later this year on its forthcoming drilling campaigns.”
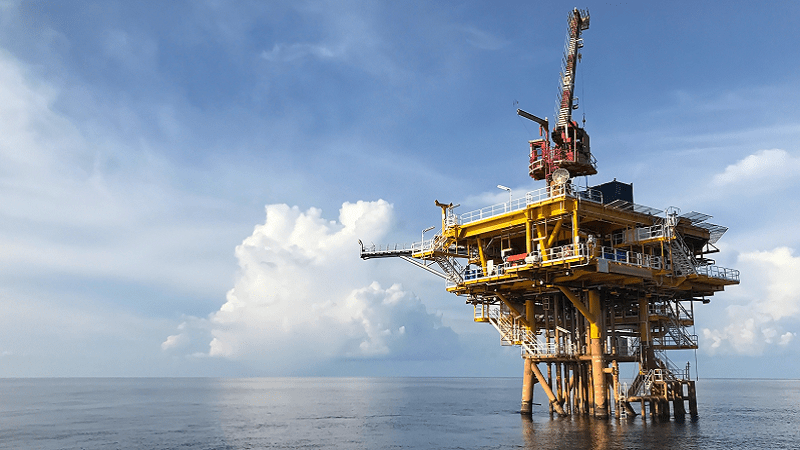
- Region: North Sea
- Date: May, 2021
Archer Oiltools has been awarded a plug and abandonment (P&A) campaign by Wintershall Noordzee B.V across 2021 and 2022. The scope awarded to Archer is to perforate, wash, and provide cement and formation integrity testing tools, services, downhole tools on tubing conveyed, and plugs-cutters for 22 wells with an option of another 20 wells.
Hugo Idsøe, Vice President of Archer Oiltools, commented, “Over the last decade Archer has delivered a high number of P&A and Slot recovery operations to our customers in the North Sea with great success. This contract is a milestone for the southern part of the North Sea and a testimonial of all the good work that we have done for Wintershall Noordzee B.V. over the last three years.”
“Our team have delivered excellent performance and we continue to prove that Archer’s Oiltools is an industry leader for smart and robust solutions in markets where well integrity, reliability and time savings are of upmost importance.”
“With a broad portfolio of products and services within P&A and Slot Recovery, Archer is in a unique position to deliver lower carbon solutions to our clients. Through our development of new technologies and solutions, we are rapidly adapting to and embracing the sustainability focus on lower emissions,” Idsøe added.
Archer has been carving a formidable presence for itself in the North Sea in recent months with this announcement coming soon after its acquisition of DeepWell, a leading Norwegian well intervention company focused on high-tech based wireline service. DeepWell commands one of the most modern wireline unit fleets on the Northern Continental Shelf and holds a strategic long-term contract in the light well intervention market, making a fine addition to Archer’s portfolio. It is therefore no surprise that the company was awarded another contract by Wintershall Noordzee B.V. and it is highly likely more work will be coming its way in the future.
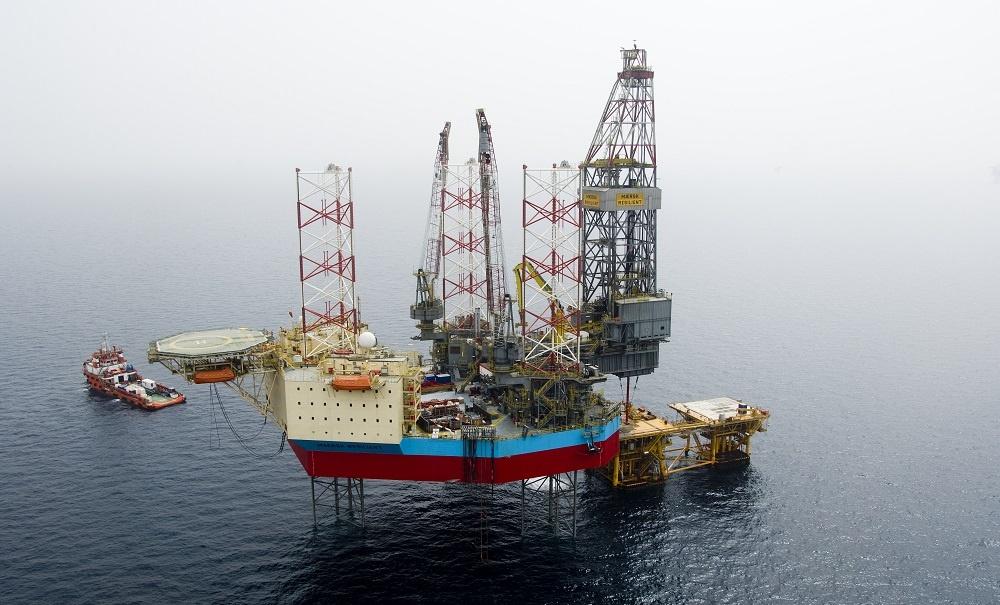
- Region: North Sea
- Date: May, 2021
Serica Energy plc, a British independent upstream oil and gas company with operations centred on the UK North Sea and gas accounting for over 80% of its production, has encountered difficulties in the drilling of the Columbus development well, located in the North Sea, 35km north-east of the Shearwater production facilities.
The Columbus development well was spudded in mid-March and drilled, as planned, to a total measured depth of 17,600ft by the Maersk Resilient heavy duty jack up rig. A 5,900ft horizontal section was drilled through the reservoir formations of the upper forties and encountered a sequence of sands and shales, in line with pre-drill expectations. The well required sand screens to be installed to prevent fine particles being produced and difficulties were encountered while running the screens so that it was ultimately not possible to install them.
As a result, the reservoir section of the well will be side-tracked and re-drilled, using data collected during initial drilling to optimise its trajectory and avoid the difficulties encountered running the screens in the original well. The additional operations are expected to take around 3-4 weeks at a net cost to Serica of around UK£3mn.
While this has raised the expense of the operation, these recent developments are not expected to affect the timing of production start-up, which is still projected during Q4 2021. Serica stated that further updates will be provided on each project when flow test data is available.
Mitch Flegg, Chief Executive of Serica Energy, commented, “Whilst frustrating, the additional operations on Columbus are not expected to affect the timing of first production, and the economic returns of the project remain very attractive for the company.”
A recent Competent Person’s Report estimates the Columbus gross undeveloped 2P reserves to be in excess of 14 million boe and, once production begins, the average gross production forecast is projected to be around 7,000 boe per day, of which over 70% is gas.
Rhum 3 update
Serica also provided an update on the R3 Intervention Project, situated on the Rhum field, which commenced in October. The company stated that the R3 well has now been cleared of all equipment installed when it was originally completed in 2005. Reservoir access has been regained, thus allowing new completion equipment to be run in preparation for production.
The new completion is currently being installed prior to performing a flow test on the well, which is expected to be carried out in June. A diving support vessel has been contracted to install the subsea control equipment required so the well can start producing in Q3 2021.
More Articles …
Page 30 of 37
Copyright © 2024 Offshore Network