North America
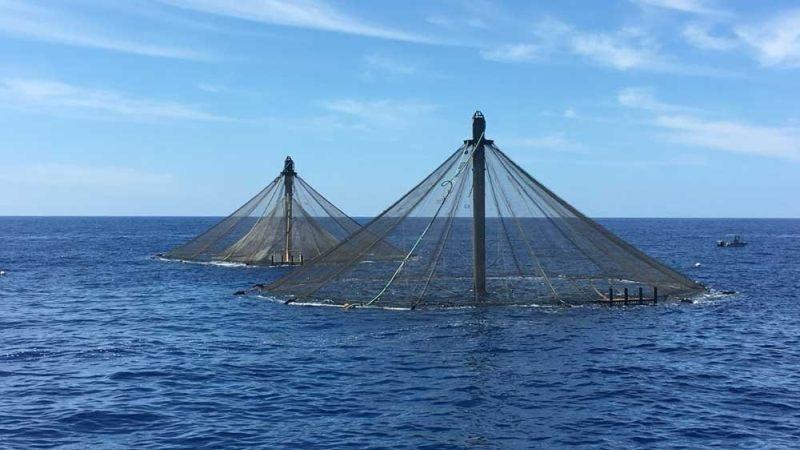
- Region: Gulf of Mexico
- Topics: Decommissioning
- Date: Feb, 2022
With many oil rigs being decommissioned in the Gulf of Mexico each year, plans of converting rigs for alternatives like offshore multi-trophic aquaculture (finfish, oyster and algae) production and renewable energy, has been on the cards for oilmen and fisheries alike.
US regulations already allow US Gulf of Mexico platforms to be used for other purposes, apart from oil and gas production. Right of Use and Easement (RUE) permits for alternative uses of offshore platforms have been granted in the past and these regulations would also allow for aquaculture and other marine-related activities. Leasing of Gulf of Mexico areas for wind power is expected to begin in late 2022.
Aquaculture is an increasingly important source of nutritious and sustainable seafood for people worldwide. Globally, aquaculture production must double by 2030 to keep pace with demand. This increase in demand for aquaculture products, food security considerations, and job creation has generated the need for skilled workers.
Ivan Puckett, one of the founders of Blue Silo Aquaculture LLC, while speaking to The Fish Site, said, “Our objective is to find as many uses as possible because we will need an income stream to maintain and operate the platforms. There’s enough space on these installations for several projects and the more operations we can have, the better it is.”
Aquaculture is one of the sectors they see as having the most promise for extending the useful shelf life of the platforms.
Puckett believes aquaculture is promising. “The water quality and oxygen levels are good and disease transmission is low. However, travel expenses to and from the platforms are high, the weather can be challenging, with hurricanes not infrequent and living arrangements are more challenging,” he added.
Kent Satterlee, co-founder Blue Silo Aquaculture LLC, informed that the company is planning to initially install a grid of 12 of Innovasea’s SeaStation pens and add another 12 at another platform site.
The SeaStation design includes the ability to be raised above the waterline in calm weather, exposing the netting to naturally defoul in the sunshine and then be submerged to a depth where they will avoid the full impact of any hurricanes or storm events that happen to pass.
“Innovasea also has expertise, materials, equipment and relationships to provide nearly all of the support aspects of the operation. Video monitoring, feeding systems, various marine and atmospheric monitoring devices, design and technical support, IT integration capabilities and much more,” Satterlee noted, while speaking to The Fish Site.
Puckett added that the company is looking into multi-trophic production; with a mixture of finfish, seaweed and oysters, and the University of Miami will be researching species selection.
In this scenario, the mooring grid for the SeaStation pens could also host the downlines for oysters and algae. The platform structure could also serve as host for the downlines.
D&A GOM 2022
At D&A GOM 2022, the offshore community is set to reunite face-to-face to discuss the challenges and opportunities marking decommissioning and abandonment in the region, listen to sessions delving into current complex situations and network to help each other optimise their strategies. To find out more, download the brochure: https://offsnet.com/da-gom/conference-brochure
Or contact:
Joseph Watson
Project Manager
Offshore Network Ltd.
t: +44 (0) 20 3409 5720
e:
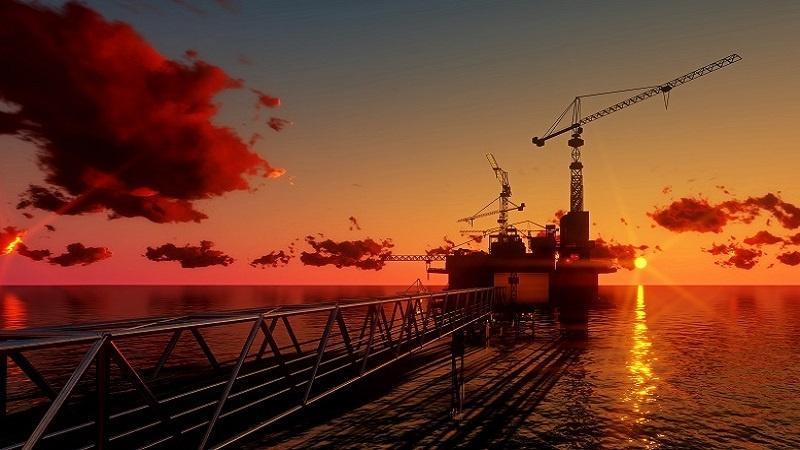
- Region: Gulf of Mexico
- Date: Feb, 2022
W&T Offshore, Inc., an independent oil and natural gas producer, has closed its acquisition of oil and gas producing properties in federal shallow waters in the central region of the Gulf of Mexico from privately-held ANKOR E&P Holdings Corporation and KOA Energy LP.
The assets are located in the Ship Shoal 230, South Marsh Island 27/Vermilion 191, and South Marsh Island 73 fields. After normal and customary post-effective date adjustments, cash consideration of approximately US$30.2mn was paid to the sellers using cash on hand.
The acquisition will add internally-estimated proved reserves of 5.5 million barrels of oil equivalent (Boe) (69% oil) and proved and probable, or 2P, reserves of 7.6 million Boe (75% oil).
It will add more than 50 gross producing wells (average working interest of 80%) across three shallow water fields to the company’s working interests in 41 producing fields. In such a developed field many of these assets will likely be closing in on their twilight years, presenting an opportunity for well intervention service providers to maintain their production rates and extend their life-span.
Tracy W. Krohn, Chairman and Chief Executive Officer, commented, “Now that we’ve closed the transaction, we’ll begin working on realising the synergies we’ve identified and maximising the value of these assets. We will continue to seek other accretive transactions that can further enhance shareholder value.”
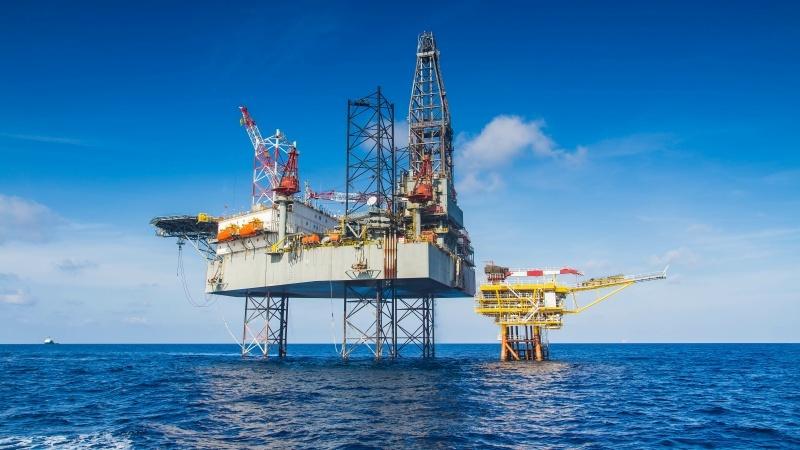
- Region: Gulf of Mexico
- Topics: Decommissioning
- Date: Feb, 2022
The US Department of the Interior has announced that US$1.15bn in funding is available to states from the Bipartisan Infrastructure Law to create jobs cleaning up orphaned oil and gas wells across the country.
This is a key initiative of President Biden’s Bipartisan Infrastructure Law, which allocated a total of US$4.7bn to create a new federal programme to address orphan wells. Millions of Americans across the country live within a mile of an orphaned oil and gas well.
The historic investments to clean up hazardous sites will create good-paying, union jobs, catalyse economic growth and revitalisation, and reduce dangerous methane leaks.
“President Biden’s Bipartisan Infrastructure Law is enabling us to confront the legacy pollution and long-standing environmental injustices that for too long have plagued underrepresented communities,” said Secretary Deb Haaland. “We must act with urgency to address the more than one hundred thousand documented orphaned wells across the country and leave no community behind. This is good for our climate, for the health of our communities, and for American workers.”
Plugging orphaned wells will also help advance the goals of the US Methane Emissions Reduction Action Plan, as well as the Interagency Working Group on Coal and Power Plant Communities and Economic Revitalization, which focuses on spurring economic revitalisation in the hard-hit energy communities.
Nearly every state with documented orphaned wells submitted a Notice of Intent (NOI) showing interest in applying for a formula grant to fund the proper closure and cleanup of orphaned wells and well sites.
The Department released the amount of funding that states are eligible to apply for in Phase One, which includes up to US$25mn in Initial Grant funding and a quarter of the total Formula Grant money available for the 26 states that submitted NOIs. These allocations were determined using the data provided by states from the NOIs and equally considers the following factors required by the Bipartisan Infrastructure Law.
In the coming weeks, the Department will release detailed guidance for states to apply for the Initial Grants. These resources will allow state officials to begin building out their plugging programs, remediating high-priority wells, and collecting additional data regarding the number of orphaned wells in their states.
D&A GOM 2022
At D&A GOM 2022, the offshore community is set to reunite face-to-face to discuss the challenges and opportunities marking decommissioning and abandonment in the region, listen to sessions delving into current complex situations and network to help each other optimise their strategies. To find out more, download the brochure: https://offsnet.com/da-gom/conference-brochure
Or contact:
Joseph Watson
Project Manager
Offshore Network Ltd.
t: +44 (0) 20 3409 5720
e:
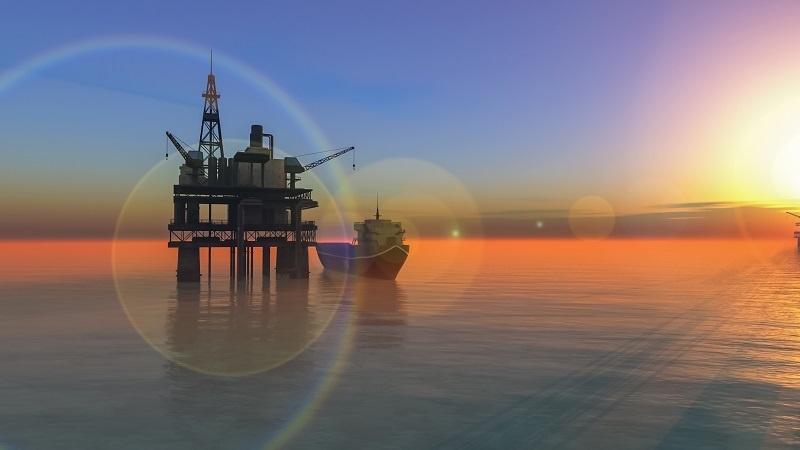
- Region: Gulf of Mexico
- Date: Jan, 2022
As it approaches the five-year anniversary of its first contract with PRT Offshore, Interventek Subsea Engineering has announced that it is shipping out their latest Revolution in-riser safety valve order.
This is for a new 4-1/8” 10,000psi, shear-seal valve, designed for slimline well access with an outer diameter of 15-1/8.
The slimline Revolution valve is the first of its kind and reflects a growing need for technology which is easily scalable to suit the individual challenges of different subsea intervention projects. Like all Interventek’s products, it has undergone extensive testing and meets the latest API 17G industry standards.
The valve will be used for intervention operations in the Gulf of Mexico in more than 2,450 m (8,000 ft) depth of water with an integral intervention arrangement, using a surface BOP for well control with direct vertical well access to the wet xmas trees below. The Interventek slimline valve will be used in conjunction with this arrangement to enable safe and efficient well access.
PRT Offshore already have an impressive fleet of eight additional Interventek Revolution valves in service, which have built up an extensive track record of deployments in the GOM over the last few years.
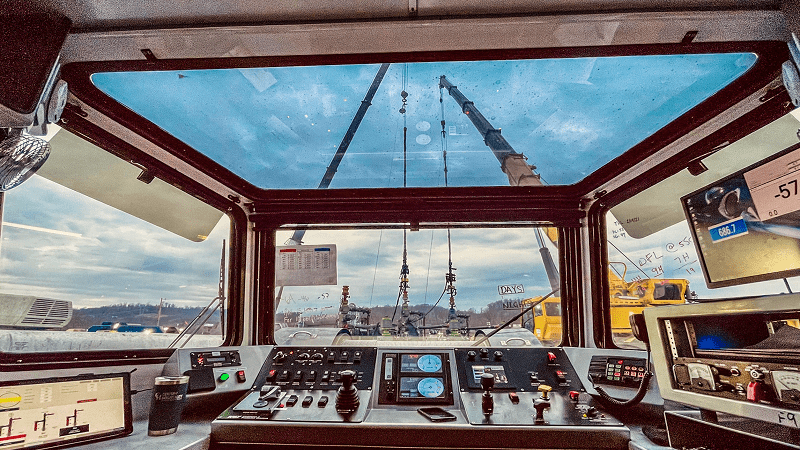
- Region: Gulf of Mexico
- Date: Dec, 2021
Intelligent Wellhead Systems (IWS), a leading supplier of digital technologies that improve oil and gas well completion operations, has announced that oil and gas company algorithms to improve completions may now be combined with hydraulic fracturing, wireline, and pressure control job data.
By doing this, customised workflows, threshold alerts, and other analytical applications can be created.
The company’s inVision Technology Platform features a powerful data acquisition and control system, iHub, which is a proven digital technology infrastructure at the wellsite for hydraulic fracturing and wireline operations.
The latest innovation for the platform is the ability to leverage the iHub infrastructure provided by IWS to implement operator-driven analytics on the Edge or in the Cloud. The iHub delivers field-proven data acquisition, storage, bi-directional sync, Edge computing power, and an open infrastructure to enable operators to deploy and implement their own proprietary algorithms or digital workflows on the Edge or in the Cloud.
Bob Duncan, Vice-president of innovation at IWS commented, “There is growing demand from E&P data science teams and completion engineers to implement their software developments on the Edge or in the Cloud. We now have a proven solution of equipment, infrastructure, and hands on the ground to make these implementations possible in a cost-effective manner.”
The inVision Technology Platform integrates engineered safety controls, automated digital standard operating procedure compliance, and Digital Handshake processes to improve the safety and efficiency of hydraulic fracturing valve activation and wireline operations.
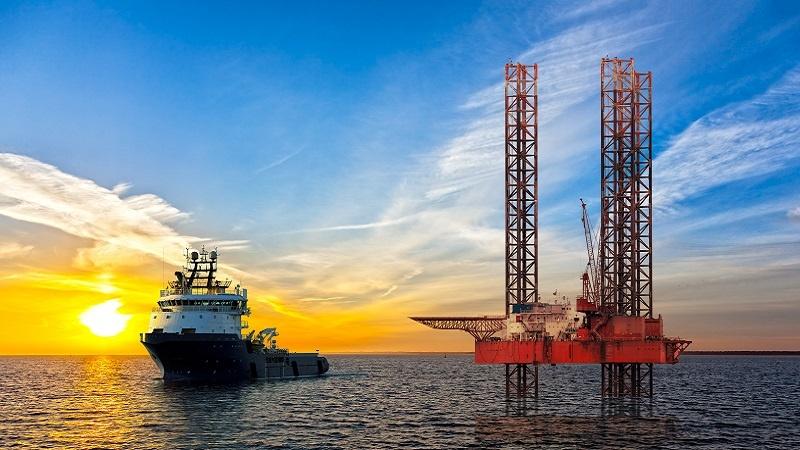
- Region: Gulf of Mexico
- Date: Dec, 2021
On the second day of the Offshore Well Intervention Gulf of Mexico 2021 conference, attention turned to technology and operational excellence and plug and abandonment, before attendees were exposed to a number of in-depth case studies.
As chairman for the second day of the conference, Nathan Wolford, Project Manager at C-Innovation, opened the proceedings by noting that in this modern world it is easy to take energy for granted. “Covid-19 saw a collapse in demand for energy products, but it got better and in 2021 we are rebounding in our energy consumption and forecasts expect that we will meet or exceed the 2019 levels (highest historical levels to date). By 2040 the forecast the energy demand will increase by 30%.
“83% of energy worldwide is derived from fossil fuels and oil is the biggest of this. As oil producers and service companies, the good news is oil and gas is the dominant worldwide energy source and will continue to be for the foreseeable future. Demand will increase by 30% over next three years, so in some ways we have an obligation to create more production and more energy.
“So we going to have to find more efficient ways to increase existing production through production enhancement mechanisms, and find safe and efficient ways to P&A ageing wells and fields and continue to develop technologies to gain efficiencies on these.”
Over the course of the day, this speakers and attendees demonstrated that they clearly had an intention to do so.
For example, one notable highlight was Zach Bruton’s presentation on the solutions that Baker Hughes has in their toolbox for use in the GOM. The Growth Lead for North America Subsea at Baker Hughes outlined the agnostic and modular tooling design programme that they have developed, introducing the Tree Retrieval Tool and the Tubing Hanger Retrieval Tool before discussing passive well monitoring technology and its possible applications in the region. The session, titled ‘Optimising Asset Retirement Through Agnostic Technologies’ was concluded with a case study from the UK and received a good reception from the audience - interest was demonstrated by the many questions that were directed towards Bruton.
Following this session with another equally engaging demonstration by Christopher Thompson, VP of Business Development at United Subsea Specialists. This young company is committed to delivering equipment to reduce critical path time, cost of operations and risk for operators. Thompson presented several innovative solutions his company has brought to the market, such as their 350t-750t Wire Line Frames, which is enabling them to achieve this commitment.
The plug and abandonment section of the day was kicked off with a panel discussion featuring representatives from Chevron, Schlumberger and Welltec. The experts explored the different types of P&A being executed within the GOM before focusing on the value that can be achieved from performing P&A from a dedicated well intervention vessel as opposed to a rig.
The last point of call was turning to case studies which, as the final section of the conference, were last but certainly not least. Highlights here included a presentation from Bruce Trader, President of MADCON Corporation, who reviewed the development and design of the Structural Composite Retrofit (SCR) Process which restores structural integrity and provides long term corrosion protection to severely corroded or damaged conductors and well casings. Trader presented a number of case studies on the SCR Process and noted that, to date, it has been used to restore the original design capacity and provide long term corrosion protection to hundreds of wells.
The final session of the conference was an engaging presentation from Welltec and Wellgrab AS on replacing conventional heavy fishing methods with light controllable intelligent tools. Garry Andrews, Senior Business Development Manager at Welltec described the solutions that Welltec provides for fishing operations, such as the Well Stoker and the Welltec’s Release Device (WRD), touched on why E-line is preferable over the convention heavy means, outlined some related case studies and finally discussed the Wellgrab AS and Welltec collaboration. Geir Magne Mo Johnsen, Founder and COO of Wellgrab AS followed this by demonstrated the capabilities of its digital well intervention robot which can be converted to fish anything inside or outside a well. The versatility and adaptability of this tool means that this is the only tool Wellgrab AS has in its tool suite.
Each session was sandwiched by networking drinks which allowed attendees, for one of the first times in nearly two years, to meet face-to-face, discuss and potentially formulate partnerships and business propositions for the future. The entertaining conference concluded with a view to returning again in the next year, hopefully when the world has made even more progress along the exhausting road to recovery.
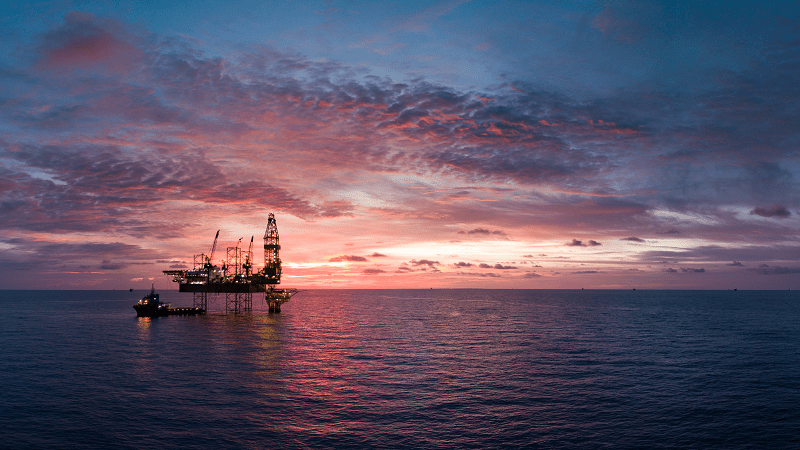
- Region: Gulf of Mexico
- Date: Dec, 2021
Returning live and in-person, the Offshore Well Intervention Gulf of Mexico 2021 conference treated assembled industry stakeholders to an informative two-day exploration of the state of well intervention in the region and examined the technology and best practices which have the potential to shape campaigns of the future.
Jim Maher, President of Trendsetter Vulcan Offshore (TVO) who co-chaired day one of OWI GOM 2021, opened the conference by noting his delight at finally being able to speak to everyone in person and emphasised that “times of great dislocation, which these clearly have been, are often the times where most innovation comes to the fore.
“As the market recovers, the intervention technologies are among the most viable as they are the closest approximation to short cycle. As we start going again, intervention technologies are certainly going to be among the most competitive for the capital available.”
Following this, over the course of the next two days, attendees were treated to a banquet of engaging sessions featuring presentations and discussions from the most influential service providers, operators, consultants, and more.
BP lead a panel discussion on how the company achieved optimal results on its ongoing RLWI campaign (which began two years ago) and the challenges it has faced and how they will continue to overcome them. Representatives from C-Innovation, Halliburton and JDR Cable Systems joined the discussion and together they explored the innovative tools, equipment and technology which could be deployed in order to achieve the most efficient intervention campaigns.
The implementation of new technology was one of the conference’s clear themes, which Charles Brooks, Technical Sales Representative from Interwell, heavily leaned into as he presented on the Interwell Barrier Verification System. This market-leading barrier assurance tool provides, as demonstrated by a case study from the GOM, time efficiency, confident and correct verification of well barrier and integrity, the ability to reduce tensile stress from pressure from pressure testing from surface (especially in fragile well constructions) and more. This solution was quoted as the most extensive downhole barrier verification the operator has performed in the region, proving its quality.
Maxim Volkov, Principal Domain Champion at TGT Diagnostics, followed closely on Brooks’ heels by introducing the Sand Flow product which precisely locates sand entry to the wellbore and provides a qualitative sand count, indentifying problem zones to help combat the serious issue of sand production. Through the use of case studies, Volkov demonstrated how the Sand Flow product, when used in tandem with Tendeka’s Filtrex solution, can localise target and fix sand issues affecting wellbores to ensure productivity is restored and integrity is maintained.
Not to be left out, Archer joined the party as Kevin Squyres, Sales and Service Delivery Manager, demonstrated the capabilities of the Stronghold Barricade, Defender and THOR solutions which can eliminate the need for milling, providing an effective alternative to traditional methods of plug and abandonment.
While new technology can bring value, it is also important to understand and asses the risk of incorporating it into intervention campaigns. This topic was covered in detail by industry experts from Schlumberger, United Subsea Specialists, Chevron and CRG Oilfield Abandonment LLC at the session focused on intervention technologies for existing field uplift.
In the following sessions on day one the sessions were dedicated to:
• Understanding the considerations when evaluating different intervention philosophies and technologies. A Baker Hughes presentation highlighted that light well intervention can achieve substantial benefits such as 55% total emissions reductions (when compared to a rig-based operation) as well as cost-saving incentives.
• The consolidation of well opportunities, where representatives from Trendsetter Engineering, BP, MADCON and TGT Diagnostics presented case studies of campaigns that have increased production and extended the profitable life span of wells as well as explored the future opportunities presented by LWI, HWO and coiled tubing technologies.
• Considering lifecycle completion. Shell, BP, PRT Offshore and Welltec associates discussed the completion design considerations; new completion and well technologies which could have an impact on the future well intervention scope; and how regional operating environment influences operations view’s on new well programmes.
• The successful application of real-time enabled coiled tubing for abandonment of a deviated well with complex anomalies. Ed Adams, Customer Engagement Coordinator at Schlumberger showcased a case study on a tricky well which was causing issues for the operator. Schlumberger deployed the ACTive CCL to detect tubing anomalies and implemented a number of solutions to return the well to safe state which was all done in days before hurricane Elsa entered the GOM.
The day was closed with a brief review of the enormous amount of material that was covered with topics such as marketing dynamics, creating value in well intervention and technology and operation considerations in particularly standing out. Before the attendees retired to the networking drinks, they looked ahead to day two and the exciting subjects that were yet to be explored.
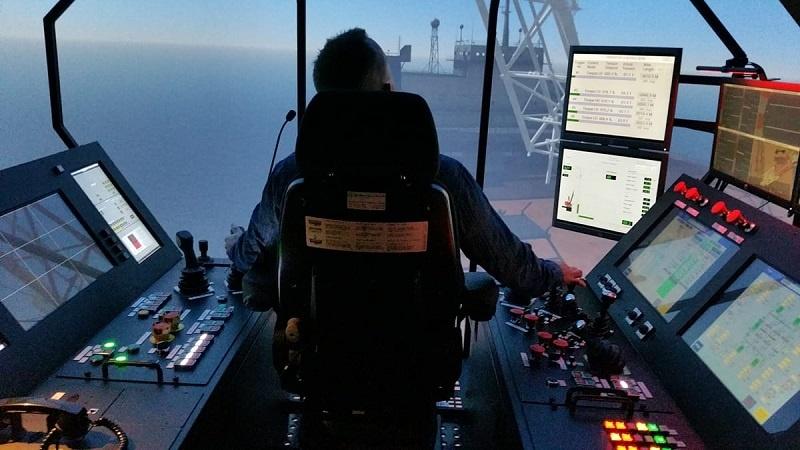
- Region: All
- Topics: Decommissioning
- Date: Dec, 2021
Kongsberg Digital has confirmed that Heerema Marine Contractors (HMC) has renewed its Long-Term System Support Program (LTSSP) contract with the company for another five years.
The LTSSP is in support of a K-Sim Offshore Crane simulation system, which features digital twins of HMC’s semi-submersible construction vessels, ships and barges.
Renewal of the LTSSP ensures Kongsberg Digital’s continued commitment to maintaining Heerema’s simulators at the leading edge of available technology. Installed in 2015 as one of the world’s most advanced offshore heavy lift crane simulators, its usage ranges from confirming feasibility of new methods and equipment to optimising efficiency and safety performance for current execution methods.
“By renewing this LTSSP we are ensuring that our clients, offshore crew and project teams continue to benefit from the most advanced simulation-based training and project preparation on the market, simulating real-world scenarios,” commented Jan Pieter de Vries, Manager Simulations and Visual Products, HMC Academy. “Kongsberg Digital have proved a competent partner, working in close collaboration with the team here at HMC to ensure that training and simulation needs are met. We are pleased to confirm our ongoing relationship.”
Heerema’s simulator platform was developed specifically by Kongsberg Digital to meet Heerema’s requirements as a leading marine contractor in offshore renewables and oil and gas, specialising in transporting, commissioning, and decommissioning offshore facilities.
The Simulation Centre is a real-time offshore environment where offshore crew and project teams examine all project aspects and associated risks. It includes two offshore crane operator domes and a bridge with K-Sim DP simulator, based on the same Kongsberg Maritime K-Pos DP systems used on HMC’s vessels. Detailed models of Heerema’s SSCVs, Heavy Lift Vessel, tugs and barges ensure realistic scenarios and enable detailed pre-mission training for heavy-lift projects.
“HMC’s renewal of this LTSSP is a clear endorsement of the capability and longevity of our maritime simulation solutions,” remarked Andreas Jagtøyen, Executive Vice President Digital Ocean, Kongsberg Digital. “Our commitment to supporting the maritime industry is not limited to providing the best technology, but also extends to ensuring that our customers gain value from their investment for years to come, through long product lifecycles and extensive service, provided by our 24/7 support network. Our LTSSP programme elevates our relationship with our customers beyond just being a vendor to rather act a trusted partner.”
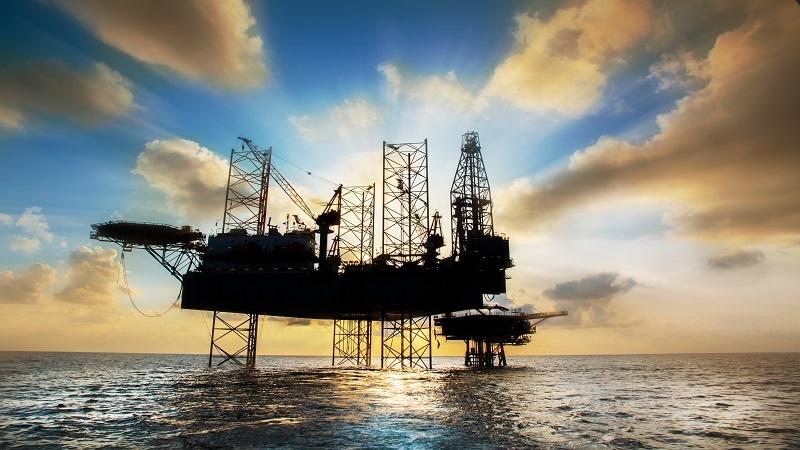
- Region: All
- Date: Nov, 2021
Helix Energy Solutions Group, Inc, an international offshore energy services company, has joined Trendsetter Engineering, Inc. in a global partnership to provide integrated hydraulic intervention services for subsea wells and flowlines.
The new partnership will integrate Trendsetter’s 15,0000 psi Subsea Tree Injection Manifold (15K STIM) and experienced personnel into Helix’s state-of-the-art fleet of well intervention vessels including the Q4000, Q5000, Q7000, the Seawell, the Well Enhancer as well as two chartered monohull vessels; the Siem Helix 1 and the Siem Helix 2.
Mike Cargol, VP of Rentals and Services for Trendsetter Engineering, commented, “This collaboration with Helix allows us to streamline contracting, improve operational efficiency and mitigate the operational and financial risks typically associated with hydraulic intervention operations. Although the initial focus is hydraulic intervention, we are excited about what the future holds for Helix and Trendsetter and look forward to collaborating further in order to provide additional value-added services to our clients.”
Jonathan Rourke, General Manager of Helix’s Subsea Systems Intervention Group, added, “We are delighted to have reached this agreement with Trendsetter Engineering, representing a collaboration between two industry leaders with expertise, experience and capabilities in the global well intervention market. This partnership will expand Helix’s intervention capabilities to further provide cost-effective and efficient alternative solutions to our end clients, and further reduce financial risks.”
More Articles …
- Enhancing production and asset lifecycle management with 3M’s Ceramic Sand Screens
- Flexibility in Design Process Brings Better Solutions for Gimbal Assemblies
- New Intervention Systems Bring Increased Efficiencies During a Challenging Economy
- Parker LORD Launches Flexible Design Tool for Fast Gimbal Assembly Modeling
Page 12 of 17
Copyright © 2024 Offshore Network